工場業務の改善ネタ6選!ネタを見つける観点や効果を最大化するポイントを解説
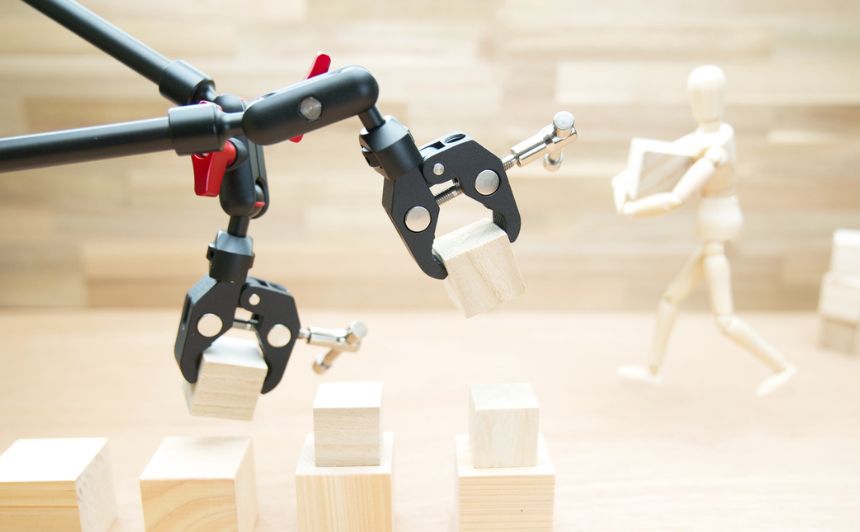
工場業務を改善するネタは様々なものがあります。ポイントさえ押さえておけば、簡単に改善ネタを見つけて業務改善を図れるはずです。
しかし、そのような意識が醸成されていない場合、改善ネタを見つけるのは簡単なことではありません。
今回は工業業務の改善ネタの事例や改善ネタを見つける観点、効果を最大化するポイントについて解説します。
工場が業務改善を図るべき理由
工場が業務改善を図るべき理由は大きく分けて次の2つです。
- 人手不足の深刻化
- 少子高齢化による生産年齢人口の減少
経済産業省が発表した2017年12月の調査結果では、製造業の9割以上の企業が人手不足だと回答しています。また、厚生労働省が発表した「令和3年 労働力調査(基本集計)平均結果の概要」によれば、製造業の就業者数は2021年では1,037万人と前年の1,045万人よりも約8万人減少しました。
少子高齢化による生産年齢人口の減少も深刻です。総務省が発表した「令和4年版 情報通信白書」によれば、生産年齢人口は1995年をピークに減少し続けています。
出生数も予想を上回るペースで低下していることから、今後も生産年齢人口の減少は避けられません。生産年齢人口の減少によって、人手不足がさらに拍車をかける中で、品質や生産量を維持・向上させるためには、工場業務を改善することが必要不可欠です。
工場業務の改善ネタ5選
工場業務の改善ネタとして次の5つが挙げられます。
- 業務のデジタル化
- 備品・工具などの管理
- 作業環境の適正化
- 品質向上
- 事故リスクの低減
それぞれ詳しくみていきましょう。
1.業務のデジタル化
人手不足が深刻化する中で注目を浴びているのが、業務のデジタル化による効率化です。デジタル化による業務効率化は様々な方法がありますが、代表的なものとしては以下が挙げられます。
- 日報のデジタル化
- チェックリスト・マニュアルのデジタル化
- 各種報告書のデジタル化
- ロボットによる自動化
従来、紙で管理されているこれら業務をデジタル化すれば、時間を問わず記入や情報共有ができるため、手間をなくすことができます。報告書の改修やデータベースの入力といった無駄な工数を省けるため、業務の効率化を図れるでしょう。
また、ロボットによって作業を自動化できれば、その作業に割いていた人員をコア業務に割くことができるため、従業員の負担軽減にも寄与できます。
ただし、上記方法はあくまでもデジタル化の初期段階に過ぎません。デジタル化が進んだ製造業の企業では、ARグラスやドローンによって点検業務をデジタル化し、さらなる業務効率化を図っています。
2.備品・工具などの管理
備品・工具などの管理を最適化することで、業務を効率化させることが可能です。備品・工具管理における改善ネタとしては以下が挙げられます。
- 工具・治具の収納場所を固定
- 使用するボルトを作業別に管理
- 吊り具の設置
工具・治具の収納場所を固定し、使用するボルトを作業別にして管理することで、目的のものをすぐに見つけることが可能です。
また、吊り具を設置すれば、工具を引っ掛けておくだけのため、取り出しやすく、戻しやすくなります。工具を戻しやすくすれば、床に放置するリスクも低減できるため、足元の安全を確保でき、事故リスクの低減にも寄与できるでしょう。
3.作業環境の適正化
作業環境の適正化も工業の業務改善につなげられます。例えば、作業環境が悪いと単純なミスが発生しやすいです。設備の配置が適正ではないと無駄な移動が発生して効率が悪くなりますし、設備不良に気付かなったり、報告していなかったりすると作業がストップする事態になりかねません。
ミスやロスの削減、業務効率化を実現するためには、設備配置の最適化や簡単に報告できる体制を構築し、作業環境を適正化していくことが大切です。
4.品質向上
品質向上につなげられる工場業務の改善ネタとしては以下が挙げられます。
- AIを活用した異常検知システムを導入する
- データロギング
人が検品を行う場合、漏れや抜けなどが発生する恐れがある他、検品精度を高めると検品までに時間がかかります。異常検知システムで検品を行えば、ミスを削減し、精度を向上させることが可能です。
システムの導入によって検品業務を効率化できれば、浮いた人員をコア業務に投入できるため、限られたリソースを有効に活用できます。データロギングを行えば、測定データをリアルタイムで記録できます。
常時、時系列に沿ってデータが記録されるため、設備の異常発生頻度や復帰までに要した時間の把握が可能です。
5.事故リスクの低減
安全に働ける現場にするためには、事故リスクを低減させる必要があります。事故リスクを低減させる工場の改善ネタは次のとおりです。
- 安全カバーの設置
- 金網の取り付けによる転倒防止
移動している機械の危険な部分に身体が入ってしまうと、事故のリスクが高まります。危険な部分に入らないように安全カバーを設置すれば、従業員の安全を守ることにつなげられます。
また、階段は滑りやすいため、転倒によるケガを起こしやすい場所です。切削水など、水を扱う場合は靴が濡れやすいため、転倒リスクも高くなってしまいます。
そのような場合は、金網を取り付けることをおすすめします。金網を取りつければ、靴底の水分が落ちやすくなるため、転倒リスクの低減が可能です。
改善提案のネタを見つけるための3つの観点
改善提案のネタを見つける観点として次の3つが挙げられます。
- 5S
- 目的
- 安全
それぞれ詳しくみていきましょう。
1.5S
5Sとは、工場をはじめとする製造現場における職場改善のための活動のことです。各要素と該当する改善ネタは次のとおりです。
- 整理:必要なもの・不必要なもので分けられているか
- 整頓:備品・工具などが使用されやすいよう整頓されているか
- 清潔:工具・治具を清潔に使用できているか
- 清掃:清掃による安全な作業環境を整備できているか
- しつけ:ルールの策定およびルールが守られているか
5Sの観点を持つことで、工場の改善ネタを見つけやすくなります。
2.目的
作業目的を明確にすることも大切です。「先輩に教えられた方法だから」「昔からこの方法だから」といった理由で、非効率な方法を行っていることも少なくありません。
この場合は、作業目的を明確にするとよいでしょう。作業目的が明確になれば、目的に沿わない作業を削減できるため、作業効率を改善させられます。
3.安全
安全という観点を持つことも大切です。「事故リスクの低減」でも触れたとおり、すべりやすい、身体が機械に挟まれてしまうというように、工場内には小さな出来事でも大きな事故に発展してしまうリスクが多く潜んでいます。
どのように改善すれば安全を確保できるのかという観点を持てば、改善ネタを見つけやすくなります。
改善提案のネタが見つらない場合の5つの対策
改善提案のネタが見つからない場合の対策として次の5つが挙げられます。
- 過去の事例を見返す
- 簡単な業務のデジタル化
- テーマの明確化
- 手間のかかる作業をピックアップ
- 業務プロセスの可視化
それぞれ詳しくみていきましょう。
1.過去の事例を見返す
過去の事例を参考にするのもネタが見つからない場合の対策です。他社や他部門の事例を参考にすることで、改善提案のネタが見つかる場合があります。
ただし、他社や他部門の事例が必ずしも自部門とマッチするとは限りません。そのため、闇雲に導入するのではなく、自部門はどうだろうかという視点を持ち、参考になりそうなネタを精査・導入していくことが大切です。
2.簡単な業務のデジタル化
改善ネタが見つからない場合、デジタル化できそうな小さな業務に目を向けるとよいです。工場業務全体で改善ネタを考えた場合、視野が広がりすぎて、ネタが見つからないということが良くあります。
報告書のデジタル化や情報伝達方法をチャットツールに変更するなど、簡単にデジタル化できる業務はないかという視点を持つとネタを見つけやすくなります。
3.テーマの明確化
簡単な業務のデジタル化に少し似ていますが、テーマを絞ってみるのもおすすめです。漠然と改善提案を出すといっても、ネタは中々見つかりません。
デジタルや納期、コストなど、ネタを出しのテーマを明確にすることで、具体的なイメージを膨らませやすくなり、ネタを見つけやすくなります。
4.手間のかかる作業をピックアップ
手間がかかる作業だと思っていても、何も言わず黙々と作業している方は多いです。そのため、手間のかかる作業はなにか聞き込みを行い、ピックアップしてみるのも1つの手段です。
移動が手間、設備の配置が適切ではないといったことを多くの従業員が感じていれば、改善することによって業務を効率化できる可能性があります。
5.業務プロセスの可視化
マニュアルやチェックリストなどに記載されていない小さな業務は少なくありません。そのため、細かい部分まで業務プロセスを可視化してみると、無駄な作業が発生していたり、意外な作業が紛れていたりしている可能性があります。
改善提案のネタが見つからない場合、業務プロセスを可視化してみることで、新しい発見があるかもしれません。
改善ネタの効果を最大化するための3つのポイント
改善ネタの効果を最大化するためのポイントとして次の3つが挙げられます。
- 目的意識を持たせる
- 業務負担が増えていないか経過観察する
- 現場の声に耳を傾ける
それぞれ詳しくみていきましょう。
1.目的意識を持たせる
改善ネタの効果を最大化するためには、目的意識を持たせることが大切です。経営陣が業務改善に力を入れていても、従業員がただ上司に言われたからやっているという意識では、効果を最大化することはできません。
また、従業員に改善ネタを挙げてほしいと依頼しても、目的意識を持っていないと、ただアイデアを挙げるだけで十分な効果は期待できません。改善ネタの効果を最大化するためには、なぜ改善しなければならないのか目的を共有し、従業員に目的意識を持たせる必要があります。
2.業務負担が増えていないか経過観察する
改善ネタを元に業務プロセスを変更した際、業務負担が増えていないかしっかりと経過観察することも大切です。業務のデジタル化は業務効率化できる有用な手段の1つです。
しかし、ツールの操作が不慣れな方が多い職場の場合、ツールの操作を覚えることで手一杯となり、かえって効率が悪くなるリスクがあります。また、操作を覚えることが負担となってしまい、モチベーションの低下にもつながりかねません。
このような事態を回避するためには、業務負担が増えていないか経過観察を行い、負担が増えている場合は別の方法を検討する必要があります。
3.現場の声に耳を傾ける
現場の声に耳を傾けることも改善ネタの効果を最大化するためには欠かせないポイントです。経営陣や管理者が見つけて立案したアイデアは、現場の状況に適していないことも少なくありません。
また、いきなりすべての業務を改善しようとすると、従業員がついていけず、計画が頓挫してしまうリスクもあります。計画を頓挫させずに改善ネタの効果を最大化させるためには、現場の声に耳を傾け、状況に適した改善策を実施していく必要があります。
工場業務を改善する手順
工場業務を改善する手順は次のとおりです。
- 目的の明確化
- 課題の洗い出し
- 洗い出した課題に優先順位をつける
- 改善案の検討・実施
- 効果測定を行い必要に応じて改善を実施
洗い出した課題をすべて解決することはできません。そのため、業務改善を行う目的に沿って、課題に優先順位を付ける必要があります。
また、改善案を実施したから終了というわけではありません。工業業務をより良いものにしていくためには、定期的に効果測定を行い、必要であれば改善を加えながら、最適化していくことが大切です。
まとめ
人手不足の深刻化や少子高齢化による生産年齢人口の減少によって、工業業務の改善は最重要課題となっています。備品・工具などの管理や、業務のデジタル化など、工場業務の改善ネタは豊富なため、ポイントさえ押さえておけば、工場業務の改善は十分図れるでしょう。
ただし、いきなり全業務の中から改善ネタを見つける場合や、業務改善する文化のなかった工場の場合、改善ネタを見つけるのは簡単ではありません。当記事で解説した改善ネタを見つける観点や、ネタが見つからない場合の対策を参考にしながら、業務改善の意識を芽吹かせていくことが大切です。