生産効率を向上させる5つのポイント!その理由や手順も解説
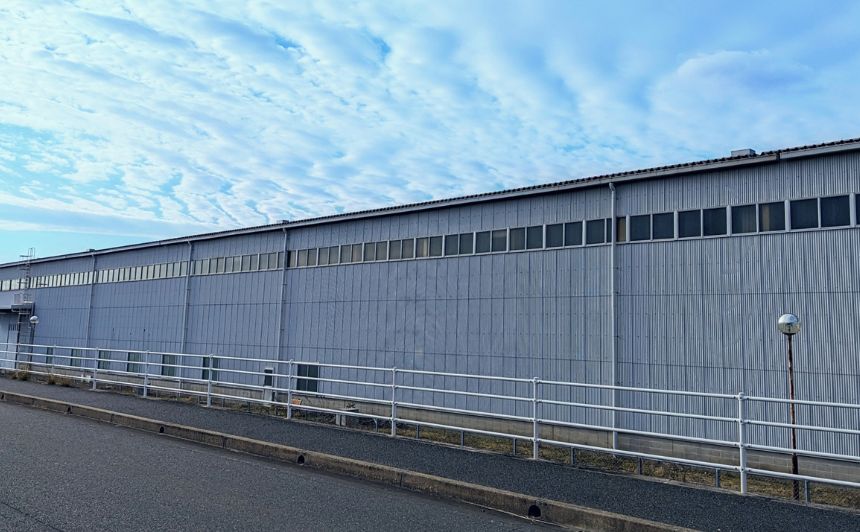
グローバル化による市場競争の激化や少子高齢化による労働人口の減少などの影響で日本の生産性は低下しつつあります。生産性を維持・向上させながら、利益を確保していくためには、生産効率の向上が欠かせません。
今回は生産効率を向上させるポイントや向上させなければならない理由、向上させるための手順について解説します。
生産効率とは?
「生産効率」とは、人的・経済的な投資への効果のことです。生産効率は高い方が良いと思うのが一般的ですが、市場は常に変動しているため、一概にそうとは言えません。
例えば、繁忙期と閑散期で分かれる製品があった場合、製造計画は過去の実績などから見込み数を算出します。しかし、実際の需要が見込みを下回ったにもかかわらず、生産効率を上げることだけ考えてしまうと、大量の在庫を抱える事態になりかねません。
したがって、闇雲に生産効率を上げるのではなく、市場の需要に対して、適切に調整していくことが大切です。
生産性との違い
「生産性」とは、「コストに対してどれくらいの出来高があったのか」を把握できる指標です。生産性は「アウトプット(算出)÷インプット(投入)」で算出可能です。
アウトプットは生産量などの産出物、インプットは労働力や原材料などの生産要素を指します。仮に150個の製品を10人で生産した場合の生産性は15、15人で生産した場合の生産性は10となります。
生産効率と生産性の関係性
似て非なるものである「生産効率」と「生産性」ですが、非常に密接に関わっています。例えば、個別の生産性を向上させた場合、売掛品や仕掛品といった在庫が増加します。
在庫が増加した場合、在庫の保管場所確保や在庫管理といったコストが増加するため、生産効率が低下します。つまり、むやみに生産性を向上させてしまうと、生産効率が低下するという事態を招くわけです。
したがって、生産性の向上と生産効率の最適化を両立させるためには、目先の生産性や生産効率ではなく、稼働率や標準時間、市場の需要などを踏まえて総合的に判断・改善することが求められます。
生産効率の種類・求め方
生産効率を考える際は、以下2種類に分けて把握する必要があります。
- 人作業
- 機械設備
ここではそれぞれの算出方法について詳しくみていきましょう。
人作業における生産効率
「人作業における生産効率」を確認する時は一般的に「1人あたりの出来高数」を使用します。1人あたりの出来高数は「出来高数(アウトプット)÷人数」で算出可能です。
例えば、15人で150個の製品を製造している状態から、15人で200個を製造できる状態となれば、1人あたりの出来高数が上がったと判断できます。大量の在庫が発生した場合を除けば、生産効率が上がったと判断することが可能です。
機械設備における生産効率
「機械設備における生産効率」を考える際に使用されるのが「可動率(べきどうりつ)」です。可動率とは、機械がどれくらい正常に動いているかを表すことができる指標で、以下の計算式で算出できます。
「実稼働時間÷総運転時間(休憩・引継ぎといった公の設備停止時間を除いた時間)」
例えば、1時間で250個の製品を製造できる設備があった際、この設備を10時間可動させた場合、2,500個を製造できる計算となります。しかし、設備の不具合やオペレーティングエラーなどで機会が止まることもあるため、計算どおりに製造できるとは限りません。
機械をチョコチョコ停止するという意味で、チョコ停とも呼ばれていますが、チョコ停が頻繁に行われると、実際の稼働時間は少なくなります。可動率を算出することで、設備がどれくらい効率良く動いていたかを確認することが可能です。
生産効率を向上させなければならない3つの理由
生産効率を向上させなければならない理由として次の3つが挙げられます。
- 市場競争の激化
- 少子高齢化
- 労総生産性の国際比較順位の低下
それぞれ詳しくみていきましょう。
1.市場競争の激化
現在、国内市場だけでなく、グローバル競争が激化しています。そのため、日本は海外勢と比較すると生産性は低いにもかかわらず、海外企業が開発している製品に機能面などで勝ちながら、利益を確保していかなければなりません。
以上の点から、大企業だけでなく、中小企業も生産性や生産効率も考慮していく必要があります。
2.少子高齢化
生産性や生産効率を向上させなければならない理由の1つが「少子高齢化による労働人口の減少」です。現代の日本は少子高齢化が急速に進んでおり、2065年には日本の総人口の4割が65歳以上となるといわれています。
労働人口が減少していく中で、今後も生産体制を維持し、企業を存続させるためには、生産性や生産効率に焦点を当てていかなければなりません。
3.労総生産性の国際比較順位の低下
製造業の労働生産性の国際比較において、日本は1995年時点でOECD主要29ヶ国の中で1位でした。しかし、2000年代から徐々に後退し、為替の影響もあって2015年には14位となっています。
労働生産性をこれ以上低下させないためには、生産性や生産効率向上が急務です。2015年には日本経済再生本部が「ロボット新戦略」を打ち出し、産業用ロボットを導入する企業も増えています。
現場・工場の生産効率を向上させるためのポイント6選
現場・工場の生産効率を向上させるためのポイントとして次の6つが挙げられます。
- 設備レイアウトの無駄を省く
- 業務プロセスの改善
- データの数値化
- 3Mの削減
- ツールの導入
- 5Sを活用した効率化
それぞれ詳しくみていきましょう。
1.設備レイアウトの無駄を省く
現場・工場の設備レイアウトは生産の流れで考えがちです。しかし、作業者の手間・コストを考慮すると、無駄が発生していることも少なくありません。
したがって、製品の評価・仕上がりや単なる生産性・生産効率の数値だけでなく、実際に作業する人の立場になって、設備レイアウトの無駄を省くことが大切です。
2.業務プロセスの改善
業務プロセスの改善も生産効率を向上させるには欠かせないポイントです。制作手順は現状のままで問題ないか、昔からの慣習に縛られて無駄な手間が発生しているかなどの観点から業務プロセスを見直すとよいでしょう。
また、社内で生産性・生産効率向上の意識が薄い場合は、研修などを実施して、従業員の意識改革を行うことが大切です。
3.データの数値化
データを数値化して可視化するのも生産効率を上げる有効な手段です。デジタルツールを活用すれば、従来ならば把握できなかったデータを数値化できます。
データを数値化すれば、無駄が発生している部分はどこかが分かるようになるため、具体的な改善策が立てやすくなります。また、ツールを上手く活用すれば、設備だけでなく、稼働状況や労働状態、健康状態などの管理も可能となるでしょう。
4.3Mの削減
3Mの削減も生産効率を上げるポイントです。「3M」とは、ムリ・ムダ・ムラのことを指します。
例えば、無駄な報告・ルールがないか、待機時間が長くなっていないかなどを見直すことで、生産性の向上が可能です。近年はデジタルツールや産業ロボットなど、機械化して自動化する業務も増えています。
設備も上手く導入しながら、人材だけには頼らない生産体制の構築が必須だといえるでしょう。
5.ツールの導入
ツールの導入も生産効率を上げる方法の1つです。近年は在庫管理システムなどの業務を効率化できるツールが増えてきました。
これらのツールを有効活用することで、業務を効率化することが可能です。前述のとおり、ツールを活用すれば、様々なデータを数値化して把握できます。
これらのデータを分析に活用すれば、精度の高い需要予測が行えるため、生産性や生産効率の適正化を図れます。
6. 5Sを活用した効率化
現場・工場の生産を効率化する手段としておすすめなのが「5S」の活用です。5Sとは、次の頭文字を取ったものです。
- 整理:必要物と不要物を仕訳し、不要物は処分する
- 整頓:必要な機器や材料を素早く取り出せるように整頓ルールを定める
- 清掃:作業後の清掃をする他、機材メンテナンスも定期的に実施する
- 清潔:整理・整頓・清掃を心がけて、常時清潔な状態を維持する
- しつけ:上記4Sが実施されるようにルールを作成し、現場に浸透させる
5Sを上手に活用しながら、効率化を促進していきましょう。
生産効率を向上させる手順
生産効率を向上させる場合は次の3ステップです。
- 目標値の明確化
- 社内で共有
- 従業員のサポート・ケア
それぞれ詳しくみていきましょう。
1.目標値の明確化
生産効率を向上させるためには、目標となる数値を明確にすることが大切です。目標を明確にする際は、はじめに自社の最終目標を設定しましょう。
最終目標を設定したら、次に部門ごとに細かい目標値を設定していきます。項目としては「売上」「人件費」「原材料費」「仕入高」などが挙げられます。
ただし、必要な数値・項目は業種や部門によって異なるため、必要な項目・目標値は部門ごとに適したものを設定しましょう。ただし、目標値が高すぎると、従業員のモチベーションが低下し、生産効率が低下してしまうため、注意が必要です。
2.社内で共有
目標値を明確化したら、社内で目標値を共有します。共有する際に重要なのは、なぜこの施策を実施するのかを現場の従業員に理解してもらうことです。
現場の従業員は生産効率を左右する重要な要素です。現場との認識にズレがある場合、生産性は向上したものの生産効率が悪くなる、個別の生産性を高めてしまい本来必要でなかった労力が発生してしまうリスクがあります。
そのため、従業員が理解していなかったり、認識にズレがあったりする場合、想定しているほどの効果を得られません。以上の点から、目標値や施策を伝える際は、目的もセットにして伝えるようにしましょう。
3.従業員のサポート・ケア
生産効率を向上させるためには、従業員のサポート・ケアを行い、働きやすい環境を整備することも重要です。トップからの一方的な指示で目標・改善を行うとすると、現場からの反発に遭うことも少なくありません。
現場の従業員にマイナスなイメージを持たれたり、モチベーションの低下を招いたりしてしまうと従業員の稼働率は低下し、生産効率は向上させられないでしょう。生産効率を向上させるためには、現場の声を取り入れながら、仕組みづくりをしていくことも重要です。
情報共有コストを削減するツールとしては無線がおすすめ!
現場の生産効率を高めるツールとしておすすめなのが「無線」です。工場などの現場は大きな音が発生していることが多く、大声を出しても声が届かない場合があります。
また、複数人との連絡を取る場合、スマホだと複数人に連絡が取れないため、情報共有しにくいです。無線を使用すれば、大きな音が発生している現場でも耳元ではっきりと聞き取りできます。
また、複数人に対して一斉連絡することもできるため、スムーズな情報共有が可能になり、生産効率の向上を図れるでしょう。ただし、無線によって通信できる範囲は異なるため、通信距離に適した無線を選ぶことが大切です。
また、一般的な無線はスマホのようにお互い会話しながらコミュニケーションを取ることができません。お互いの息を合わせて作業しなければならないような場合は、相互コミュニケーションが取れる「同時通話無線」の導入を検討することをおすすめします。
まとめ
生産効率は高い方が良いという考えが一般的ですが、市場需要が下回っているにもかかわらず、生産効率をただ上げてしまうと、大量の在庫を抱える事態になりかねません。そのため、生産効率は市場の需要に合わせて、適切な数値に調整することが大切です。
生産効率を向上させるポイントとしては「設備レイアウトの無駄を省く」「業務プロセスの改善」「データの数値化」などが挙げられますが、情報共有コストが原因であれば、連絡ツールとして「無線」を導入するとよいでしょう。
ただし、無線は交互通信が基本であり、種類によって通信できる範囲が異なります。したがって、通信範囲や通信状況に適したものを選ぶようにしましょう。